Nuclear I&C Modernization: The Future is Digital
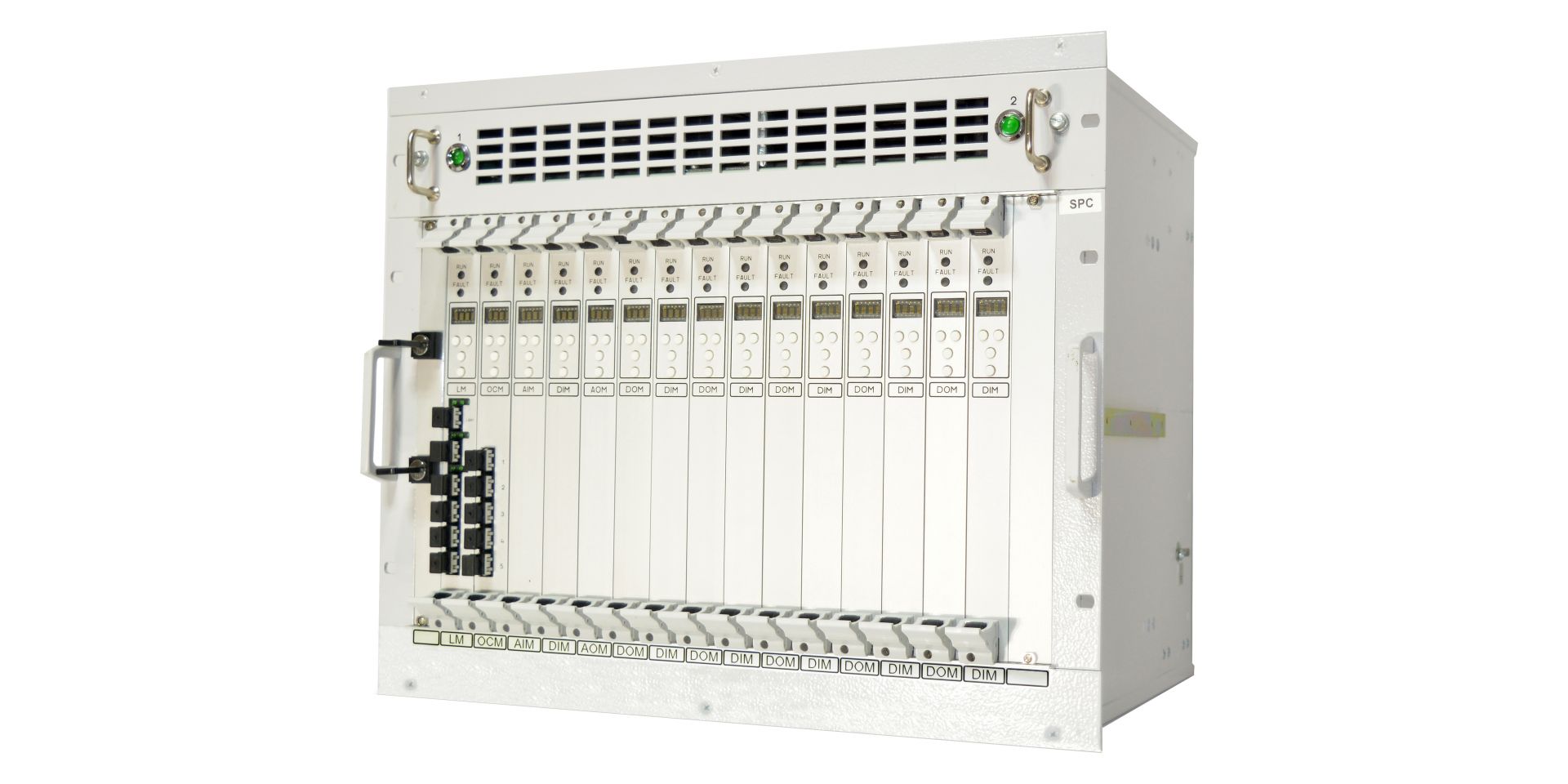
As the U.S. nuclear industry moves into plant life extension and subsequent license renewals, the modernization of safety instrumentation and control (I&C) systems holds significant potential to transform plant operations. Automated system diagnostics, equipment health monitoring, and performance indications reduce the need for manual surveillance activities and enable condition-based maintenance, resulting in improved system reliability and reduced maintenance costs. Despite these benefits, adoption of digital I&C systems for safety-related applications across the domestic nuclear fleet has been slow. U.S. nuclear power plants that do choose to embrace the transition from analog to digital are in good company; international plants have successfully implemented digital safety systems for more than a decade. Furthermore, digital safety systems are also the first choice of the growing small modular reactor (SMR) and advanced reactor (AR) communities.
Why digital I&C?
The benefits of this digital transition are numerous. The flexibility of digital I&C technology – coupled with the higher capacity of its modular equipment – allows plants to implement enhanced digital I&C architectures that can increase reliability and availability, simplify maintenance and testing, eliminate failure vulnerabilities in the current system designs, and reduce the number of hardware components in existing l&C systems by up to 80%. Further, replacing analog with digital also supports long-term plant modernization objectives by resolving numerous parts obsolescence issues – an industry-wide challenge.
Digital I&C functionality provides plant operators with the ability to automate operations and reduce maintenance, ultimately resulting in lower maintenance costs. Self-testing, diagnostic, and monitoring features enable early detection of problems, simpler troubleshooting, and shorter repair times; these improvements lead to a corresponding increase in I&C system availability. By reducing direct maintenance efforts dedicated to I&C systems, plant personnel can focus on other critical tasks – improving the plant’s overall workforce utilization.
By implementing digital I&C technology, nuclear power plants can improve system reliability and streamline operations while lowering maintenance costs and supporting industry modernization and plant life extension initiatives. Simply put, digital I&C can enable the transformation and modernization of plant operations.
Digital I&C Modernization in Operating Reactors
Safety-related I&C design for existing nuclear power plants is complex. The plants’ non-passive designs require numerous redundant safety systems, equipment, and operating procedures; all incorporated into the plant’s design basis. As a result, upgrading an existing plant’s I&C systems is complex, time-consuming, and expensive. Consequently, Safety I&C modernization projects have evolved to varied scope and scale depending on a plant’s individual needs and existing challenges.
Tactical I&C System Replacement: These projects focus on replacement of a single protection or control system with digital I&C technology, typically to address maintenance and/or obsolescence concerns.
Limited-Scope I&C System Modernization: This type of project expands upon Tactical I&C System Replacement by addressing obsolescence in multiple systems. This approach involves increased utilization of the digital platform to improve plant monitoring and diagnostic capabilities.
Large-Scope Modernization: This broad-reaching modernization approach extends beyond Limited-Scope I&C System Modernization to implement a control system architecture that enables the transformation of the plant’s operations and supports the workforce of tomorrow.
Tactical I&C System Replacement and Limited-Scope I&C System Modernization projects address obsolescence in single or multiple systems and provide synergy to aggregate data collection and provide integrated system monitoring and diagnostic displays. Large-Scope Modernization projects take a comprehensive approach to digital I&C implementation and establish a broader framework for automation that reduces human error, increases visibility of plant activity, and leverages digital technology to simplify plant operations for the next generation of the nuclear workforce. Early involvement and collaboration with stakeholders from across the plant’s operations – including operations, engineering, maintenance, and licensing – is critical for Large-Scope Modernization projects to ensure that upgraded I&C technology is not only compatible with existing systems, but also supports plant-wide strategies and objectives.
For existing plants to operate long into the future, they must become digital. Existing systems are expensive and lack the features needed to transform operations. The good news is that the solutions are available, and the industry is poised to move forward.
Digital I&C in New Reactor Designs
There are currently dozens of small modular reactor and advanced reactor designs in development. For these plants, the future is now; they will be digital from day one. SMRs and ARs differ significantly from existing nuclear power plants and will require different digital I&C platform designs. These plants have passive safety features that open the door to more flexible I&C platforms with larger safety margins and simpler designs. The passive safety designs of SMRs and ARs require fewer automatic actuation functions with no automatic control or required operator actions. There is no need for active monitoring of critical plant safety functions to support near-term operator actions or emergency planning decisions. New reactor designs may have fewer regulatory requirements for safety-related support systems for I&C equipment used to mitigate design basis events, as mission times for these safety-related functions may be short and require no long-term occupancy to perform safety functions.
Despite their differences from operating reactors, the current work in SMR and AR development will benefit the digital I&C modernization of the existing nuclear power plant fleet. These new designs will encourage the development and adoption of new digital I&C platforms and applications. They will increase industry experience and comfort with digital I&C solutions. They will improve workforce knowledge and expand the number of workers with the needed skills and knowledge. Ultimately, this will reduce the risks and costs associated with modernization projects.
For Nuclear I&C Modernization, the future is digital and the future is now.
About Curtiss-Wright
As a systems integrator, Curtiss-Wright brings together the best available hardware and software components for each project. Curtiss-Wright has partnered with Radics, LLC—an international nuclear engineering company specializing in advanced, customized safety I&C solutions—to bring the RadICS digital instrumentation platform to the U.S. nuclear power market. The RadICS I&C technology is currently deployed in more than 100 safety systems in nuclear power plants in Europe and South America.
The RadICS platform forms the basis of Curtiss-Wright’s NRC-approved Digital Safety System, a functionally and technologically diverse replacement for analog and digital safety-related systems at nuclear power plants throughout the United States. The July 31, 2019 U.S. Nuclear Regulatory Commission approval of the RadICS I&C platform for use in safety-related systems in nuclear power plants paves the way for this technology at U.S. nuclear power plants.