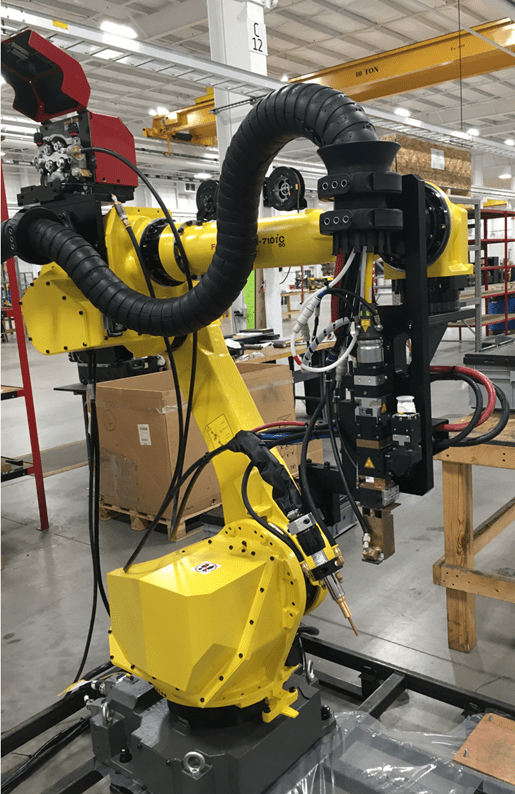
Holtec’s custom-designed hybrid laser robot. (Photo: Holtec)
Hybrid laser arc welding: The first advancement Holtec highlighted is the development of its robotic hybrid laser arc welding process, which the company says reduces the amount of heat put onto weld zones. This greatly diminishes base metal distortion and enhances metallurgical/mechanical properties in comparison to conventional arc welding, Holtec said.
The welding technology has been a focus of Holtec’s recent capital investments in the its manufacturing plants. The technology's use at Holtec’s heavy fabrication facilities in Camden, N.J., and Pittsburgh, Pa., has had an impact on the quality of its multipurpose spent fuel canisters and transportation casks, Holtec said.
The company added that the technology will be used in the manufacturing of SMR-160 components, such as the thick-walled reactor vessels, pressurizers, and steam generators.
Copper welding: According to Holtec, the company has also made manufacturing breakthroughs in the hybrid laser welding of copper. Copper, along with some other alloys, has been considered near impossible to weld with conventional arc welding techniques, the company said.
Holtec’s copper welding technology is scheduled to debut in the fabrication of a transport cask for the company’s Swedish client. The high-radiation shielding, thermal conductivity, and ability to resist aggressive environments makes copper a preferred choice for disposal canisters and other nuclear applications.
Digital radiography: Last, Holtec said it has introduced the use of digital radiography to confirm the absence of defects in the weld volume of critical welds. According to the company, digital radiography has vastly increased the sensitivity of examination capability by enabling visual access, through electronic magnification, of microstructure-level images. As an added benefit, the digital process has made remote viewing and interpretation of the radiographs possible.
Work is underway to miniaturize the digital radiography device to make it portable so that inspection of safety-related welds can occur as a routine part of in-service inspections at nuclear plants and other critical industrial installations, the company said.