Control Source Term Reduction Using Specialty Macroporous Resins
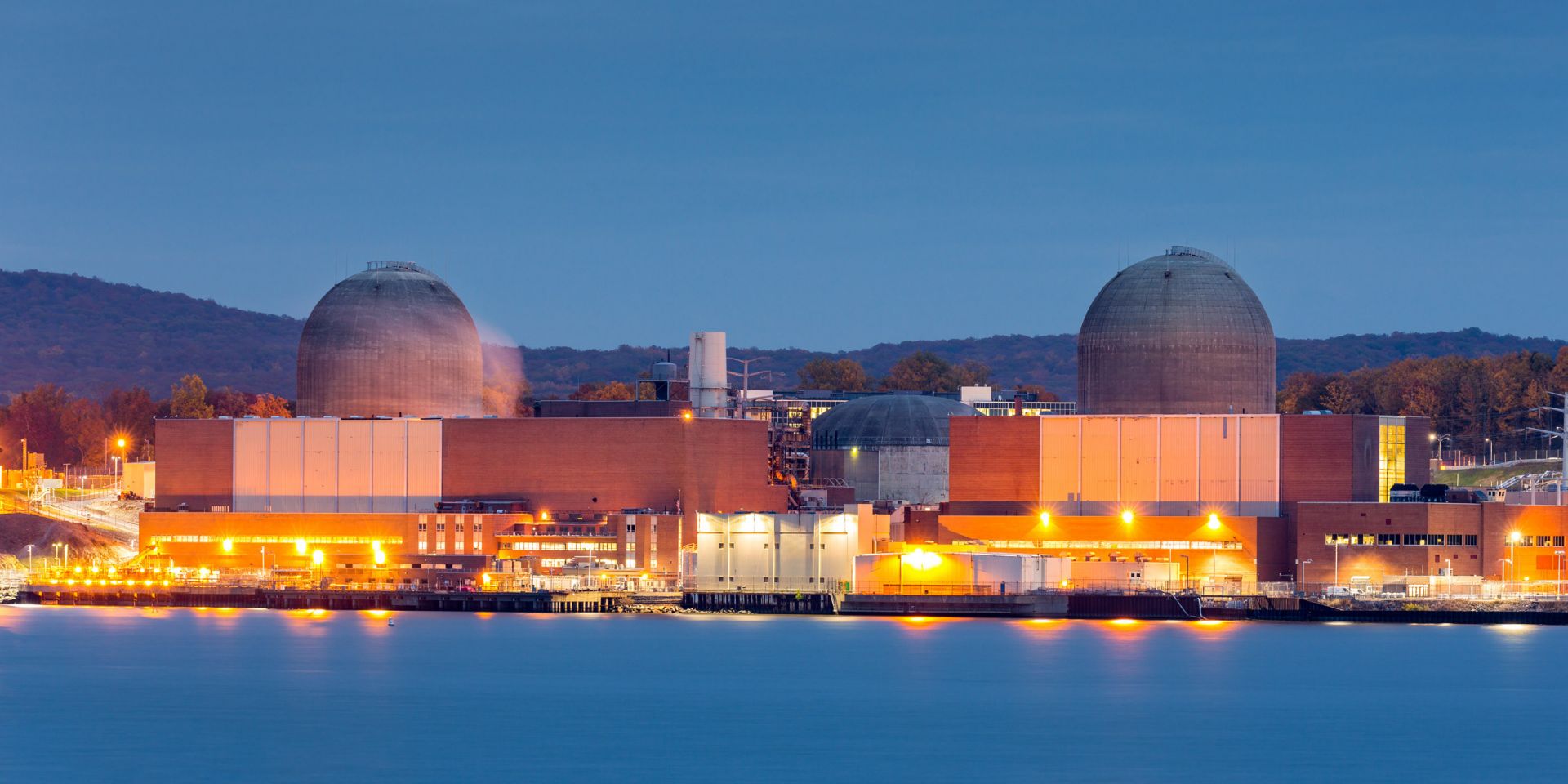
Managing plant source term for refueling outage cleanup and full power service can be controlled with the aid of specially macroporous resins. These ion exchange resins are often a cost-effective media for containing impurities in nuclear coolant, minimizing the release of contaminants and ionic leakage, all while encountering impact from oxidative chemistry and radiation. Macroporous resins continue to meet increased expectations in the industry and are considered among the best-accepted practices for nuclear plant source term minimization in standalone and layered polishing vessels.
The Macroporous Cation Resin
The NRW160 is a high-capacity macroporous strong acid cation resin. Over 30 years, this cation has successfully serviced nuclear operations, featuring a high surface area with accessibility to functional sites within the bead, and selectively holding ionic species over other cation resins. This macroporous cation is used where high ionic loading is encountered including, outage cleanup, spent fuel pool, and radwaste treatment. Macroporous cation layering provides a cation-rich bed with approximately 1.5:1 equivalence of SAC to SBA. Total equivalence for a 30cf cleanup bed has approximately 17% greater cation capacity. Cation selectivity by this macroporous cation also offers a more significant DF for Cesium and Cobalt which are isotopes released before an outage.
When macroporous cation resin is used as a mixed bed component, it can address low-level ionic polishing for cleanup. Full power CVCS and spent fuel pools mixed bed application are challenged to remove lowlevel impurities in a high background of boric acid buffered with lithium required to adjust pH. In this mixed bed, the macroporous cation selectivity is beneficial for impurities yet has a lower affinity for lithium.
The Macroporous Anion Resins
There are two macroporous nuclear grade anion resins available for addressing fine suspended corrosion products. They include NRW5010 and second-generation anion, NRW5070. These macroporous anions effectively remove ionic impurities but, more importantly, filter colloids estimated under 0.1μ in size released from the reactor, steam generator, and piping surfaces during outage cleanup. These colloids pass through voids between resin beads contributing to post-filter plugging, collecting on fuel bundles and system surfaces where they contribute to deposits, source term, and contamination events. Colloids also contribute to pump seal wear and pass to waste treatment complicating final processing. Colloids have also been the leading cause of the decontamination of casks used infuel transfer to dry storage.
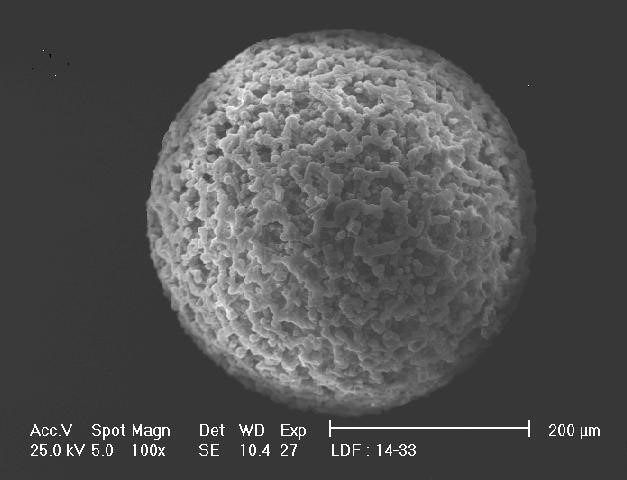
Elector Micrograph of NRW5010 Macroporous Anion
The anions recognized for filtering have large pores along with the positive charge characteristic of the quaternary amine group supporting a subtle attraction and entrapment of fines. Additionally, an alkaline nature of the anion environment allows the particulate metal to form stable complexes, which become favorable binding sites for other colloids and metal ions. These complexes adhere to the resin, which minimizes the formation of hot spots in spent resin vessels and allows waste to be slurred with minimal wastewater.
NRW5010 and NRW5070 performance features include:
a. Higher dose loading on cleanup beds
b. Use of smaller micron post filters
c. Fewer filter change-outs during cleanup
d. Fewer contamination events
e. Improved treatment of radwaste from an outage.
The Mechanism for Macroporous Layering
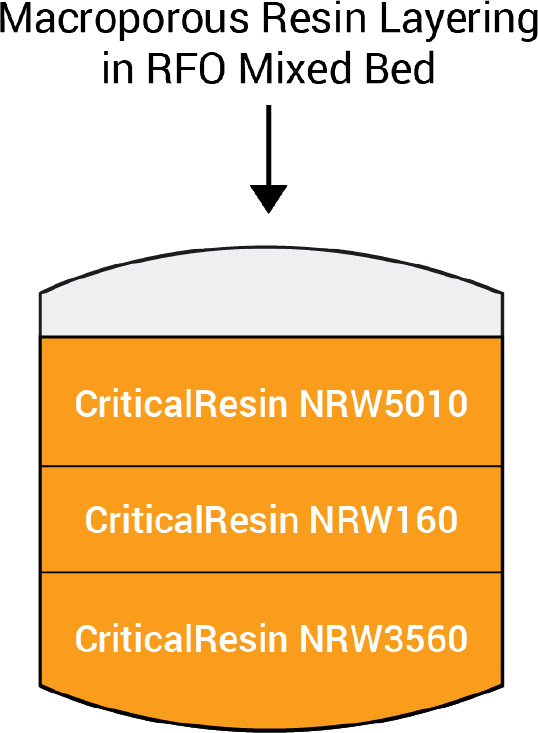
Fig. 1
Layering resin in operational demineralizers has become standard practice. This process contributes greater flexibility in addressing impurities such as colloids and higher levels of divalent isotopes, including cobalt 58 and 60. The logic of layering is placing macroporous anion on top of the cation layer and the polishing mixed bed on the bottom. This capitalizes on the specialty macroporous anion’s ability to filter colloidal, primarily metal oxides of iron, cobalt, nickel, and chromium and to maintain the stability of these oxides (see Fig. 1).
NRW5010 improves filterability when the influent solution is pH 7 rather than 5. This follows the solubility of metals such as Fe and Ni in water. With this anion resin on top, metal oxides encounter this alkaline layer, maintaining the oxide particle’s stability. If cation resin were on top free mineral acidity would reduce solution pH and effectiveness of these anions. Further work has confirmed that NRW5010 is superior to other anions in removing colloidal silica. A New England water treatment plant operates multiple beds of this macroporous anion to reduce colloidal silica from municipal drinking water.
Placing a layer of NRW160 between the anion and the mixed bed NRW3560 addresses higher loading capacity and removal efficiency (DF) of divalent cations compared to other high-capacity gel cations. This high-capacity macroporous resin reduces cation loading before the polishing mixed bed, improving overall performance and effluent quality.
Benefits of employing macroporous resin technology include:
a. Time and cost savings during outages,
b. Less total waste generation,
c. Reduction in unit source term.
Although benefits are reported by plants employing this specialty technology, macroporous resins cannot be credited solely; good chemistry, proper training, and operating efficiency are essential to achieve benefits associated with NRW5010, NRW5070 and NRW160.
Over three decades of use in nearly all nuclear systems Purolite’s specialty macroporous resins have aided in control of plant source term both for refueling outage cleanup and full power service. For more information, contact Purolite’s Nuclear Technology Expert, Chris Bailey by email: chris.bailey@purolite.com or phone: +1 954-488-0272 or visit Purolite’s Critical Resins™ on the web at: https://www.purolite.com/nuclear.