Retrieval of nuclear waste canisters from a borehole
Borehole disposal of spent nuclear fuel (SNF) and high-level waste (HLW) uses off-the-shelf directional drilling technology developed and commercialized by the oil and gas sectors. It is a technology that has been gaining traction in recent years in the nuclear industry. Disposal can be done in one or more boreholes (including an array) drilled into suitable sedimentary, igneous, or metamorphic host rocks. Waste is encapsulated in specialized corrosion-resistant canisters, which are placed end to end in disposal sections of relatively small-diameter boreholes that have been cased and fluid-filled. After emplacement, the vertical access hole is plugged and backfilled as an engineered barrier.
While the idea is gaining popularity, concerns over retrievability have yet to be fully addressed. Some countries have requirements for the retrievability of nuclear waste from the final disposal repository. Others require that waste be put permanently beyond reach as soon as possible in order to reduce proliferation risks. A requirement for retrievability is generally to allow retrieval if the repository is not performing as intended. Generally, the period of retrievability is set to be during the operating lifetime for a mined repository, which can vary. For example, for the Yucca Mountain repository in the United States, the retrievability requirement was 50 years, which was also the time during which the repository would have been open.
Boreholes are modular—they can be filled and then sealed, with additional material emplaced in new boreholes. This modularity means that each borehole is open for a much shorter period of time. A typical operational period might span from weeks to a few years, depending on the volume of waste being emplaced. This suggests that retrievability requirements could be shorter for borehole repositories.
There is also a misconception that retrieval from a borehole is more complicated than it is from a mined repository. The reality is that retrieval of objects from boreholes is done every day in the oil and gas industry. There are myriad standardized tools to accomplish the job, which can be customized for the retrieval of nuclear waste.
Testing waste retrieval
In addition to significant data on retrievability from boreholes from the oil and gas sectors, Deep Isolation has performed two field tests to show that retrieval of nuclear waste packages from a deep borehole is possible using off-the-shelf oil and gas exploration tools. Together, this data and field test results present compelling evidence that retrievability from boreholes can be assured if retrievability is desired for a given period of time.
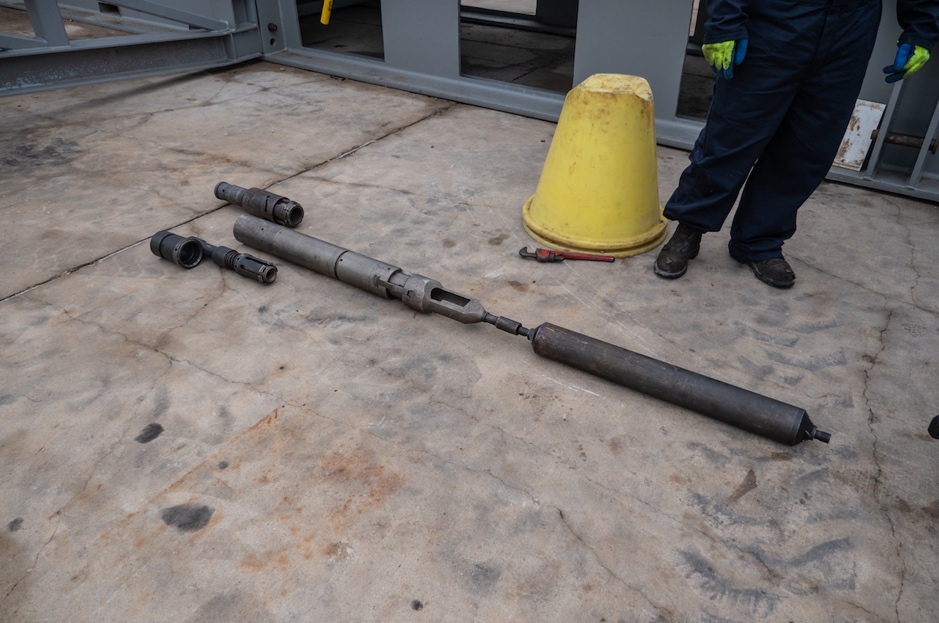
Figure 1. Disposal canister mockup is at the far right connected to a hanger. The emplacement and retrieval connectors are the smaller objects on the left side.
In late 2018 and again in early 2019, testing was performed to determine if a mock-up canister sized to accommodate a CANDU fuel bundle or cesium or strontium capsules could be emplaced and retrieved using off-the-shelf oil and gas equipment. [1]
The tests were done at an oil and gas training and testing facility near Cameron, Texas, that had an existing drilling rig, tools, and other necessary equipment to complete the test, as well as an existing well (i.e., borehole) of sufficient size.
The well was lined with casing that was cemented in place, with an eight-inch-diameter horizontal section at the bottom. The well was approximately 2,200 feet deep. Unlike mined repositories that are intended to be dry environments, the borehole is filled with drilling fluid that is engineered to maintain a balanced pressure in the well to prevent the opening of fissures or collapse of the well.
Deep Isolation used a mock-up disposal canister sized for Cs and Sr capsules that was about 36 inches long and five inches in diameter. The canister weighed about 60 pounds and had an attachment on one end to connect to the off-the-shelf lifting equipment.
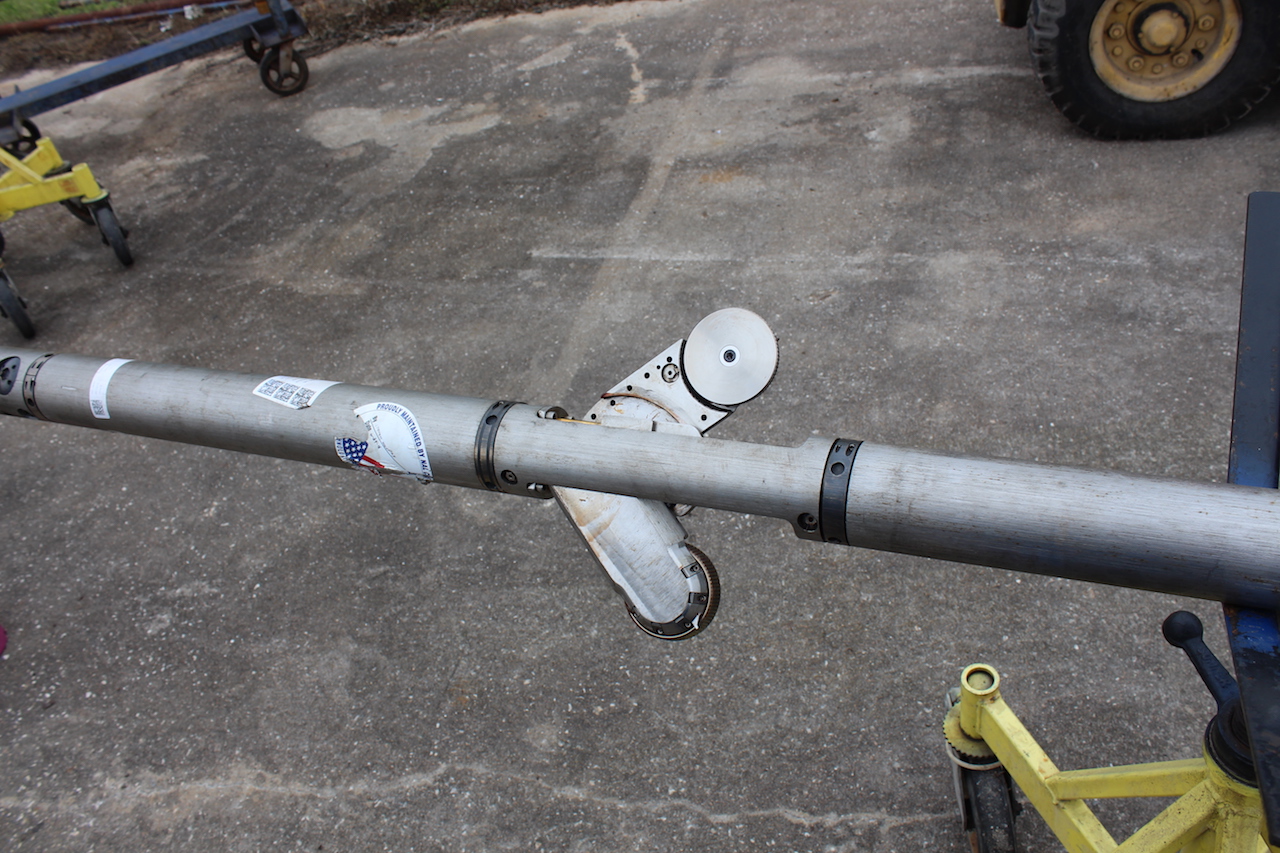
Figure 2. The wireline tractor with two wheels extended to show its position inside the casing that allows them to push the canister to the disposal zone of the horizontal borehole.
The first test used a wireline and tractor. The canister was emplaced about 500 feet into the horizontal section of the well at the full depth of 2,200 feet. Due to the light weight of the canister, a hanger was used, which allowed the canister to be anchored into position in the casing. The canister was then released and the wireline was retracted to the surface to demonstrate proper detaching. The wireline was then again lowered into the well and reattached to the canister. The hanger was disconnected and the canister was brought back to the surface with no significant damage resulting from the operation.
During emplacement, the wireline cable tension remained at about 1,000 pounds-force (lbf). The canister only weighed about 60 pounds, so this was more than sufficient force to move the canister into position. Setting force—the amount of force that can be applied by the wireline tool as the hanger was set for the canister—increased from a low of 2,000 lbf to a high of 6,000 lbf for the first two minutes, then spiked to a high of 36,666 lbf for approximately 30 seconds before returning to 2,000 lbf for the duration of the setting log. . A higher setting force ensures that the hanger is not set by accident.
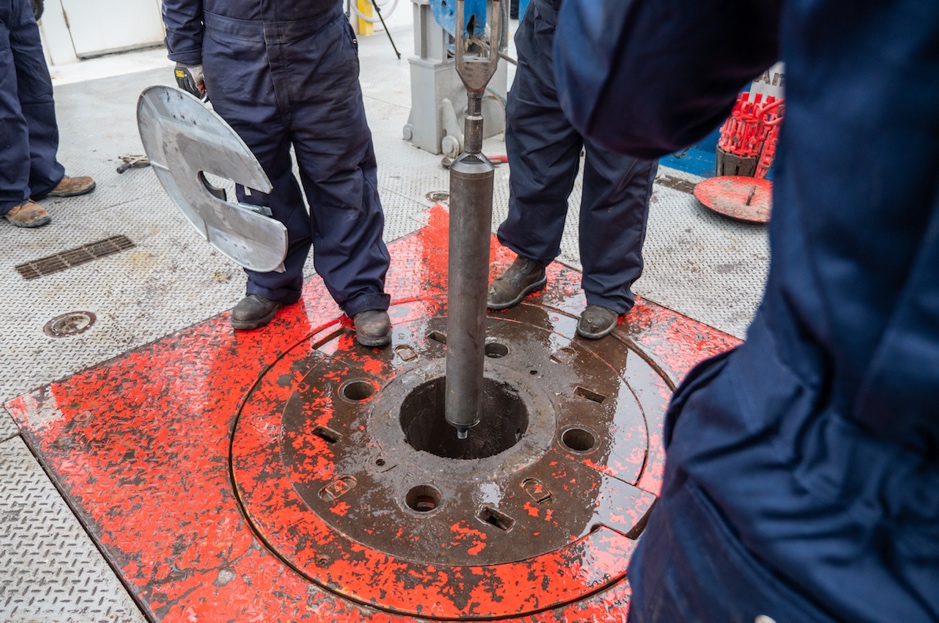
Figure 3. The canister is hanging from the oilfield tool string above an open hole in the rig floor.
During retrieval, the wireline cable tension was just under 1,000 lbf at the beginning and then lowered to 500 lbf as buoyancy effects took place and less force was required to pull the canister out of the fluid-filled well. The temperature at the bottom of the well remained about 140°F, though during retrieval, the temperature decreased to 100°F as the tool came closer to the surface. Well pressure was about 1,050 psi at the bottom of the well, which decreased to 250 psi during retrieval as the tool came closer to the surface. This is the pressure that balances the collapse and fracture pressures on the borehole.
In February 2023, a second test was conducted, with the intent of assessing and validating changes in the canister design related to the interface between the pressure-actuated lifting equipment (GS connector) and the canister lift adapter, ensuring feasibility of moving the canister to and from the rig platform, and troubleshooting any difficulties. The test was conducted at the same oil and gas training and testing facility that was used for the small-canister tests in 2018 and 2019.
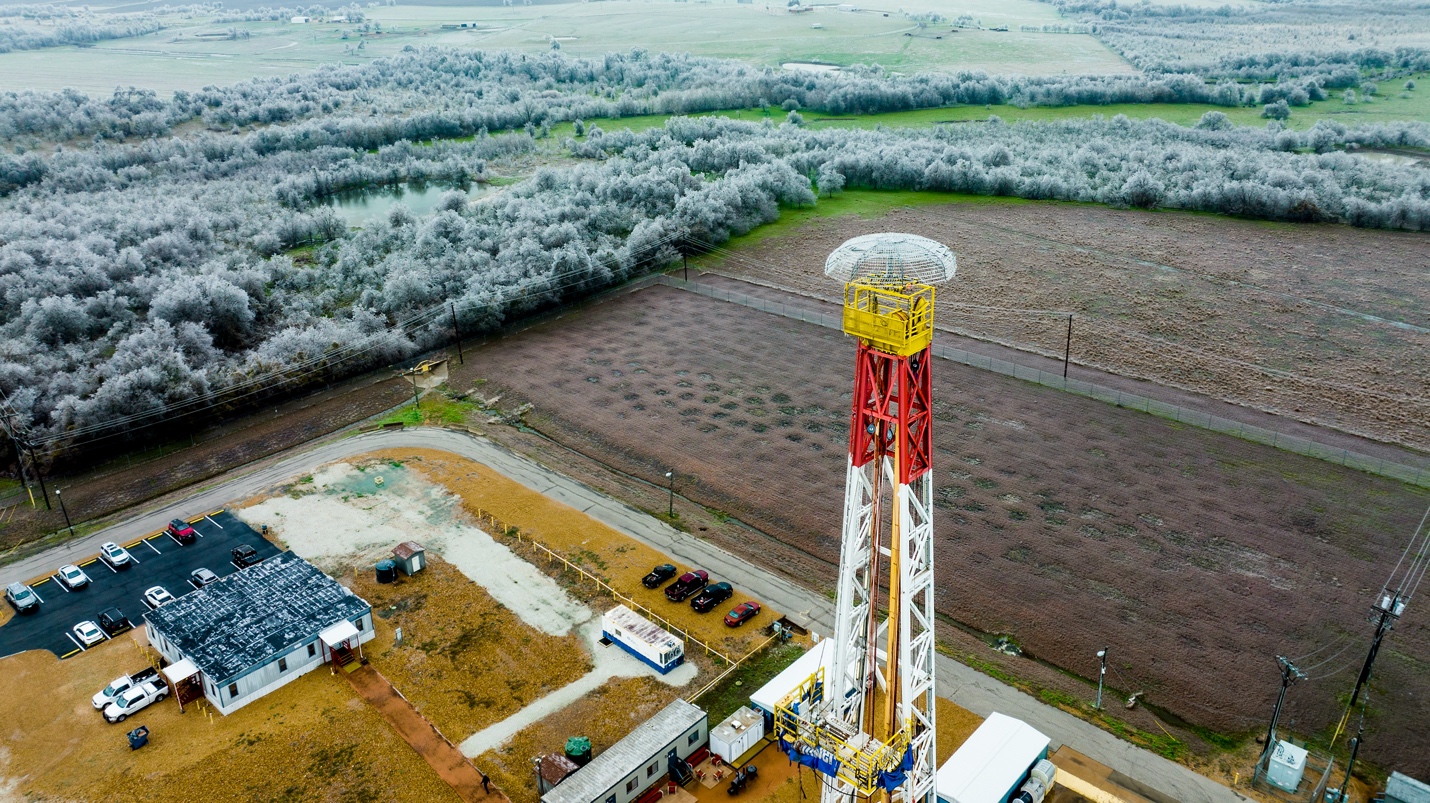
Figure 4. Aerial view of the testing facility. The trees nearby are coated in ice.
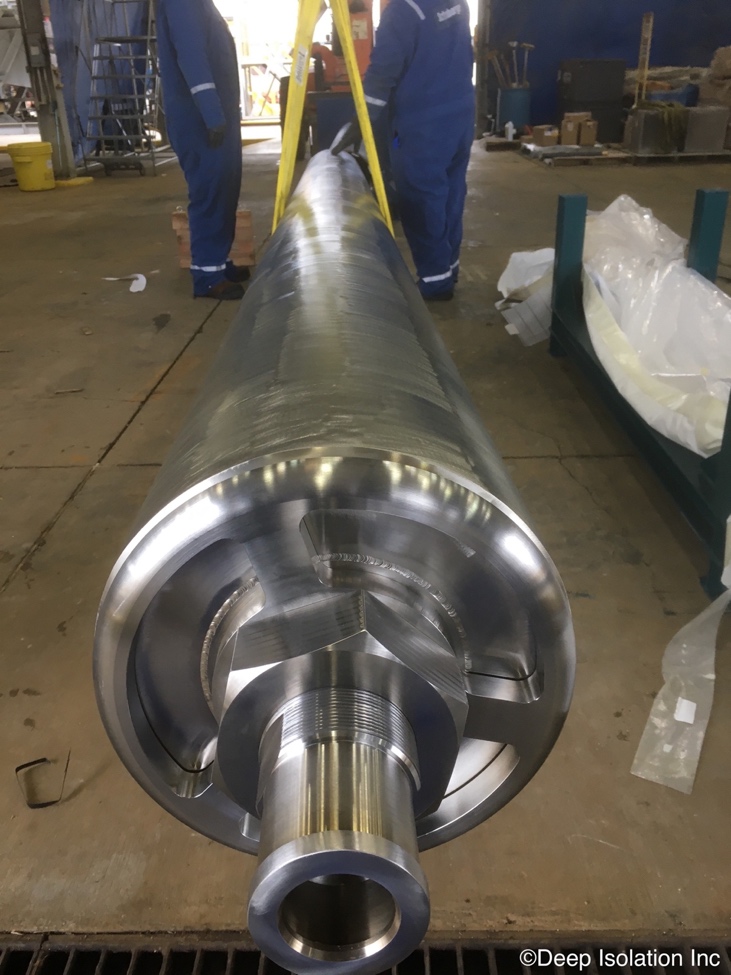
Figure 5. The full-sized mockup disposal canister used for the testing.
The lifting attachment is at the bottom of the photo.
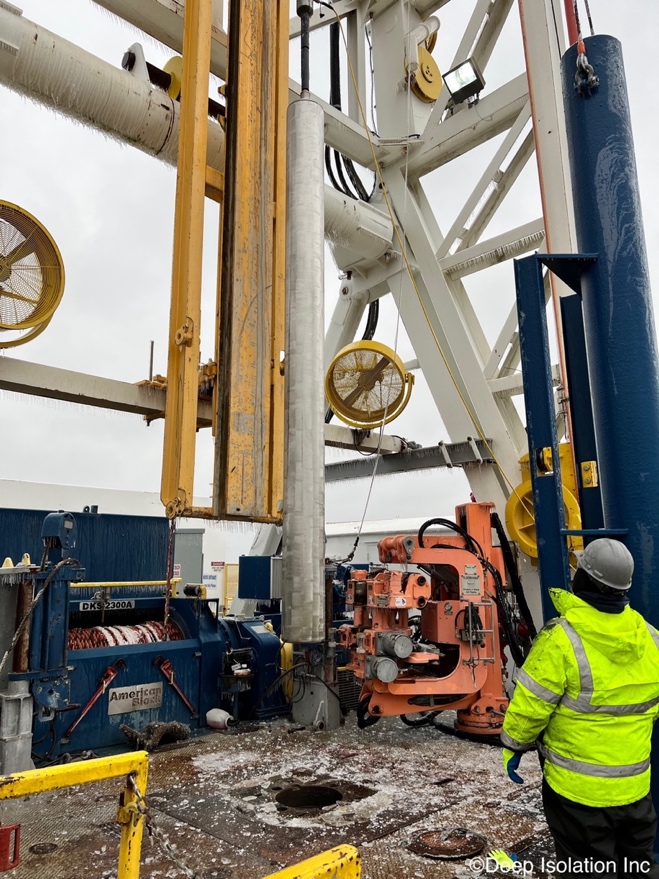
Figure 6. The full-sized canister suspended over the rig floor opening with the casing strand located beneath.
The canister is connected to the drill pipe using a GS connector.
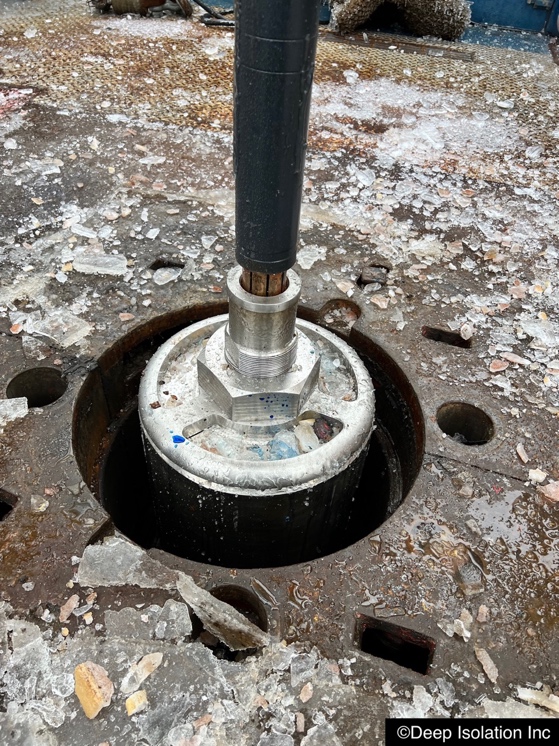
Figure 7. The canister is almost flush with the rig floor at the time of this picture.
This figure shows the GS connector engaged with the canister lift adapter.
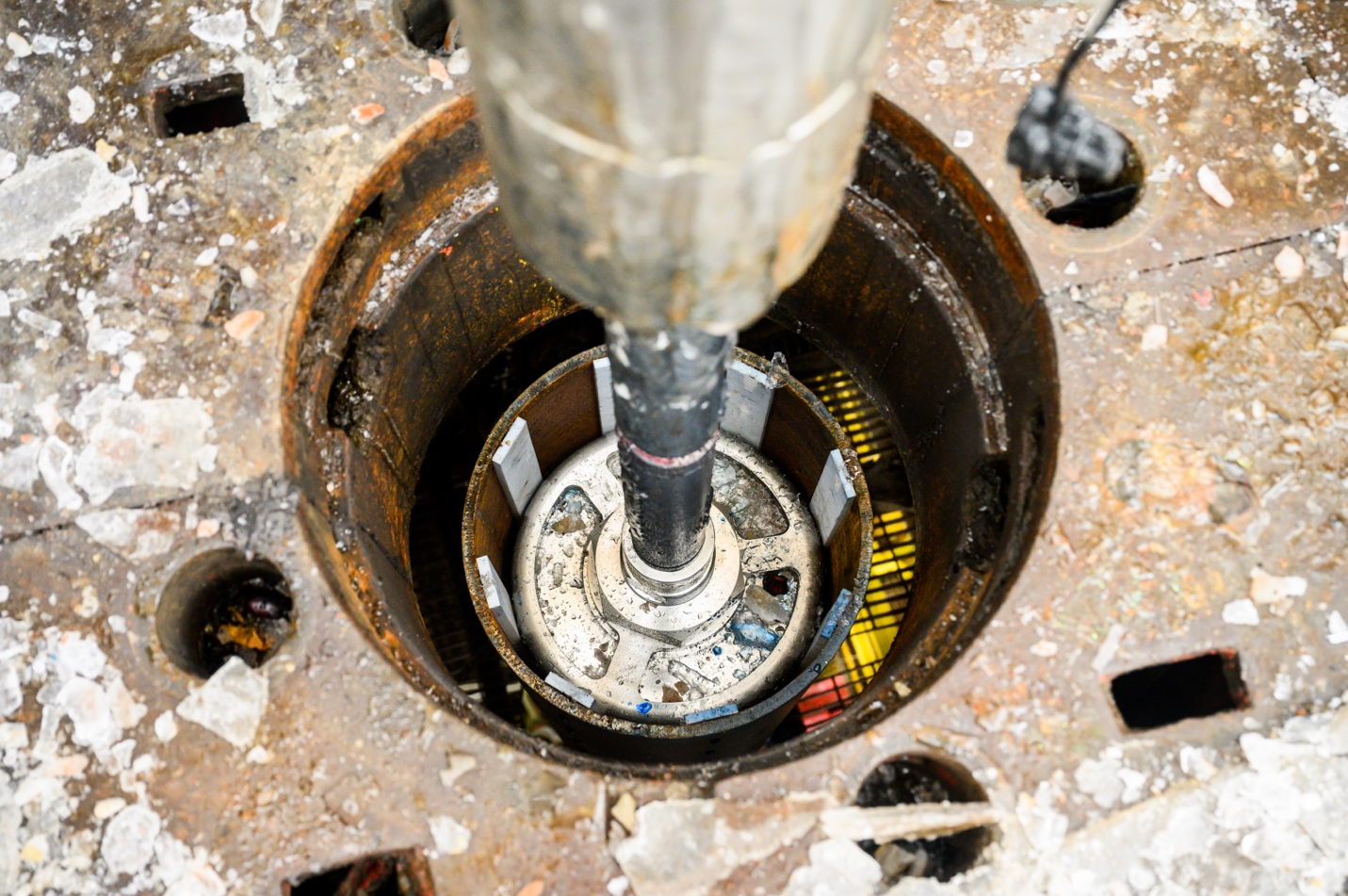
Figure 8. The full-sized canister is resting on the bottom of the casing strand below the rig floor with the drill pipe still connected.
This time, a full-sized mock-up canister (designed to accommodate a pressurized water reactor assembly) with lift adapter was connected to a drilling rig using a GS connector—a standard connector for oil field tools and equipment. Other equipment included a transfer cradle to transport the canister to and from the rig floor, a bottom cradle to simulate planned repository equipment located below the rig floor, and other standard drilling rig equipment.
The canister was about 15 feet long and 15 inches in diameter. It was weighted with a payload to simulate the heft of a commercial PWR spent fuel assembly, for a total package weight was approximately 5,000 pounds.
This test was done on a drilling rig with 18-inch casing placed between a blowout preventor at the surface and the rig floor above. The casing was not filled with drilling fluid since it was not below the surface, but the casing size was consistent with below-surface operations for the full-size canister. Drilling pipe connected the canister to the rig, and air hoists on the rig were used to move the canister into position.
The canister began in a transfer cradle in a vertical orientation and then was lifted above the transfer cradle. The cradle was removed to allow the drill pipe to lower the canister through the bottom of the rig floor and into the vertical casing strand installed beneath. Once the canister was emplaced, the GS connector was pressurized to allow for the release of the canister, and the drill pipe was retracted. Once emplacement had been completed, the drill pipe was repositioned and reattached to the canister by depressurizing the GS connector. The canister was then retrieved and removed from the casing strand, with no significant damage present as a result of the operation.
Other risky business
Concerns that have arisen with deep borehole disposal include the risk of dropping a canister into a borehole and a canister getting stuck in the borehole—potentially in the most limiting location, aligned with the aquifer zone.
Many, including Deep Isolation, have considered and taken into account these risks. During the canister design process, structural analyses were performed to evaluate multiple drop scenarios. It was found that a 20-foot surface drop onto an unyielding surface is more limiting than a drop into a vertical borehole that impacts a stack of previously emplaced canisters. In both drop scenarios, the structural integrity of the canister was maintained without any breach of the containment boundary or release of radioactivity.
Structural design analyses also have been performed to calculate a maximum allowable pull force of 20,000 pounds, should a canister be stuck. There is sufficient margin of safety to increase the pull force to 60,000 pounds without overstressing the lifting attachments of the canister. Furthermore, an event tree analysis by Sandia National Laboratories [2] effectively ruled out the possibility of a canister getting stuck in the potentially dangerous aquifer zone.
Regulatory review of retrievability
The results of the two emplacement and retrieval tests show that retrieval from boreholes is possible, but one remaining question is the duration of the period of retrievability. Current regulations regarding retrievability are more defined for mined repositories than for boreholes.
Concerning minded repositories,10 CFR 60.111(b)—which addresses retrievability of waste under “Performance of the geologic repository operations area through permanent closure” in the code Disposal of High-Level Radioactive Wastes in Geologic Repositories—states that the repository should be designed to allow retrieval “throughout the period during which wastes are being emplaced and, thereafter, until the completion of a performance confirmation program.” It also notes that emplaced waste retrieval should be on a reasonable schedule up to 50 years from initial emplacement, unless the Nuclear Regulatory Commission approves or specifies a different duration.
10 CFR 63.111(e) provides the same stipulations for the Yucca Mountain repository. The time frame for waste emplacement at Yucca Mountain, which was expected to be about 50 years, was expected to occur after waste had been in a dry storage configuration for an expected maximum of 60 years, resulting in a retrieval-driven disposal packaging lifespan of at least 110 years.
Because a compromised overpack and/or canister could result in additional safety hazards for workers in the event of a manned reentry to retrieve materials from the repository, disposal systems for mined repositories would likely need to retain canister and overpack integrity throughout the 110-year period.
Retrieval requirements for nuclear waste in various countries.
Country | Requirements |
United States | Throughout the period during which wastes are being emplaced and thereafter until the completion of a performance confirmation program and NRC review of the information obtained from such a program. |
Belgium | No decision has been made. |
Canada | Adaptive phased management includes potential for retrievability of SNF for an extended period, until such time as a future society makes a determination on the final closure and the appropriate form and duration of postclosure monitoring. |
China | No decision has been made. |
Finland | Posiva Oy included a plan and cost estimate for waste retrieval in its construction license application. Preclosure retrievability is viable for 100 years. |
France | The repository must be designed so that it is “reversible” for at least 100 years. Reversibility is a management concept that requires technical retrievability. |
Germany | Retrievability of HLW and SNF need not be provided for in the disposal concept. However, ionizing radiation shielding must be guaranteed so that waste will be manageable for a period of 500 years after repository closure. |
Japan | No decision has been made. |
South Korea | No decision has been made. However, in the conceptual-level Korea Reference Disposal System, waste packages had to be retrievable for an indeterminate period. |
Spain | No decision has been made. |
Sweden | No retrievability requirement is imposed. |
Switzerland | The retrievability of HLW has to be considered in repository design. The technical feasibility of retrieving the waste has to be demonstrated in experiments on a 1:1 scale before the repository starts operation. |
United Kingdom | No decision has been made. |
For deep borehole repositories, operational periods are expected to be significantly shorter than those for mined repositories (on the order of one year per borehole) and likely would warrant considerations for a shorter retrievability schedule, consistent with the U.S. Nuclear Waste Policy Act. Because the emplacement schedule can offer some flexibility in borehole disposal systems, monitoring the first boreholes may provide a basis for subsequent decisions to emplace the remaining waste considered for a borehole repository.
Governments round the world differ in their approach to retrievability, and no regulatory authority has determined a retrievability period solely for borehole repositories.
The IAEA’s coordinated research project to develop a framework for the effective implementation of deep borehole disposal will provide greater levels of international consensus on the purpose and nature of retrievability requirements. Given the significant nonproliferation benefits that can be gained through the ability of deep borehole disposal to put these materials permanently beyond reach, policymakers and regulators should consider that retrievability requirements should be limited to a short time frame to enable performance confirmation for the borehole repository.
According to 10 CFR 60.111, “A reasonable schedule would permit retrieval in about the same time as that devoted to construction of the geologic repository operations area and the emplacement of wastes.” Depending on inventory size, a borehole repository may take as little as one year to construct and emplace waste. Thus, a reasonable period for retrievability might be one further year. Certainly, periods significantly below the current 50-year assumptions are likely to be appropriate for deep borehole disposal.
Uncertainties, assumptions and opportunities
Though international standards for a retrievability period vary, the United States does have a consistent retrievability upper limit of 50 years from start of emplacement. Uncertainties, however, still remain. What would be the minimum retrievability period for a single borehole repository? When there are multiple boreholes at a repository site, would they be treated separately or collectively with regard to the retrievability period? And would the retrievability period influence the sequence and timing of filling boreholes?
Based on internal and stakeholder discussions and feedback, Deep Isolation is planning for retrievability as noted below:
The canister design must allow for a 50-year retrievability period within the U.S. unless a shorter time period is agreed on by the NRC.
Boreholes at a site will be treated collectively, as one repository.
The retrievability period is assumed to begin as soon as waste is emplaced into the first borehole, and backfilling and sealing will begin as early as practicable.
Deep Isolation welcomes greater public discussion on these questions and looks forward to engaging actively in the discussion.
[1] More information about the test can be found via the Deep Isolation blog at deepisolation.com/blogs/deep-isolation-marks-two-years-since-texas-technology-demonstration/. Video footage is available on Deep Isolation’s YouTube channel, at youtube.com/watch?v=3GZ4TC8ttbE.
Rod Baltzer is the chief operating officer of Deep Isolation and is a member of the Civil Nuclear Trade Advisory Committee. He has more than two decades of experience in the nuclear waste industry