The process to cut, tie, and tape each bag involves manual efforts by multiple operators. Following Administrative Safety Controls, operators can safely perform these tasks, but since the bag is the only confinement layer, incidents can still occur. Operators, in some cases, are in close proximity to this waste, which increases the risk of radiation exposure. Once the waste is transferred out, it is nearly impossible to remove packaged waste that may contain higher dosage levels. This may lead to in- increased drum disposal costs incurred by the facility. Though these are complex issues, there is an engineered solution that addresses them very effectively.
A New Approach
Central Research Laboratories (CRL), based in Red Wing, Minnesota, has developed the Waste Drum Transfer System (WDTS) utilizing the proven technology and containment of the Rapid Transfer Port (RTP). Evolving from the RTP, the WDTS provides a more efficient method to transfer hazardous waste. It combines a modified Alpha port and a mobile drum system. Electric motors raise and lower the drum, as well as rotate in and out of a locked position on the Alpha port. Acting as a standard Beta container, the drum only opens when safely attached to the Alpha through an interlock system. This drum uses a liner, which replaces the typical use of bags, sleeves or tape to provide leak-tight containment.
The Benefits
CRL has worked with the U.S. Department of Energy sites to adapt proven RTP technology to solve current waste handling and packaging problems. Replacing bag-out operations with RTP operations greatly improves operator and facility safety by minimizing and simplifying the process.
A self-docking feature allows the drum to properly align and connect to the Alpha Port. With the push of a button, a single operator can connect and disconnect the drum in less than a minute. The RTP only opens if the drum system is fully connected, ensuring containment is always maintained. Once connected, the double doors (Alpha and Beta) can be opened to safely transfer waste. The interlock system ensures the drum cannot be removed when the doors are open.
The WDTS’s drum liners eliminate all bag and tape waste from the transfer process. This significantly reduces the final TRU waste volume and operation costs. Drum radiation levels can be monitored and adjusted by utilizing the reconnect option. The system can be disconnected and reconnected multiple times to maximize containment volume and efficiently fill each drum.
Conclusion
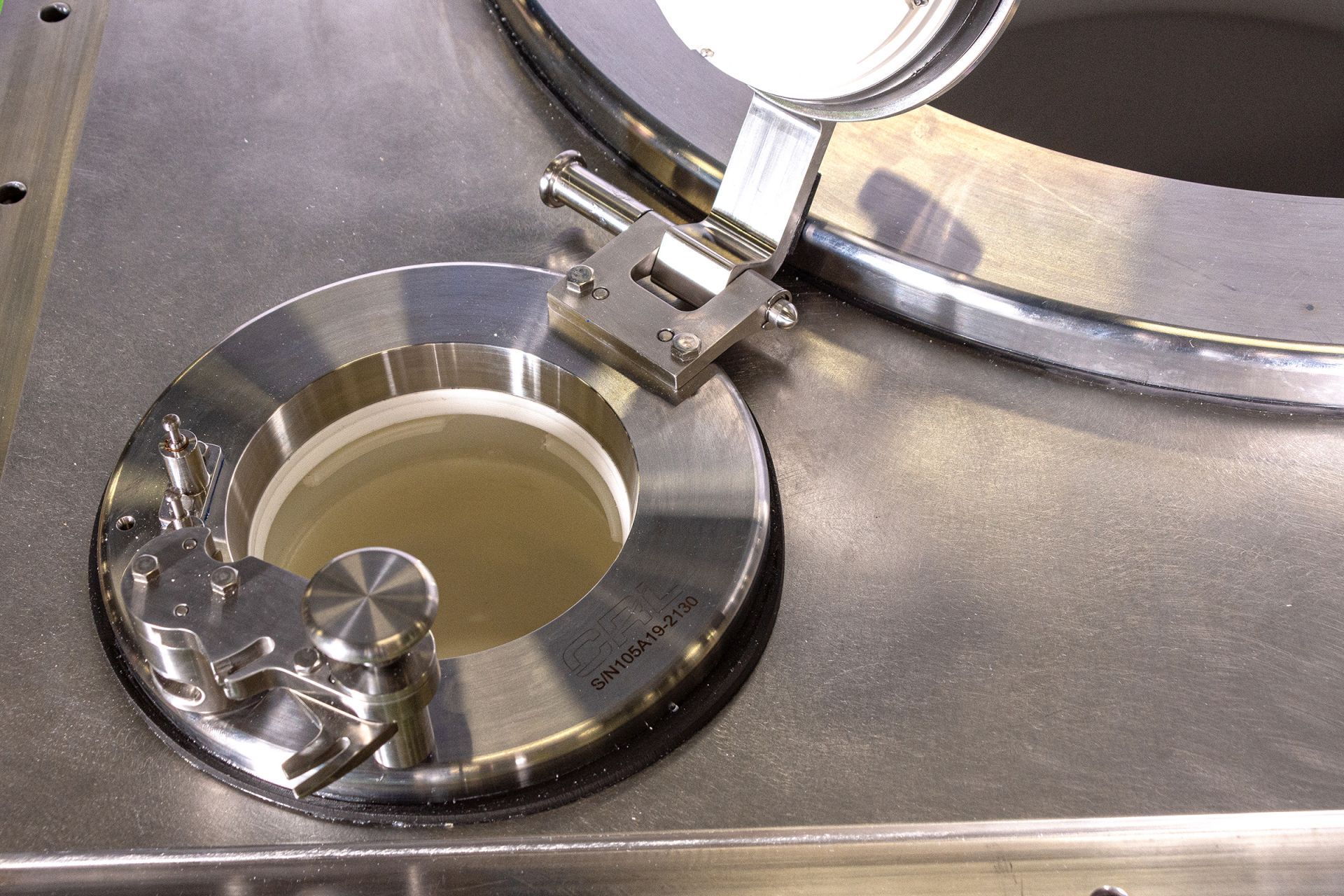
Current bag-out inefficiencies are wasting valuable space remaining at the U.S. waste repositories, and the process can put operators at risk. Using the CRL WDTS is a major step forward towards reducing the number of drums required to dispose of TRU waste. Although the cost of a WDTS is more than the bag-out materials, the significant reduction in the number of drums processed and shipped to waste repositories will cut costs. Tremendous savings are achieved by eliminating excess disposal fees on over-radiated drums by reattaching the drum and adjusting threshold levels. Increased speed and operational safety of waste packaging can also provide major savings over time. By utilizing this simple, yet revolutionary approach, facilities will be able to utilize the remaining space more economically, while maximizing operator productivity and safety.
For more information, please visit crlsolutions.com/WDTS
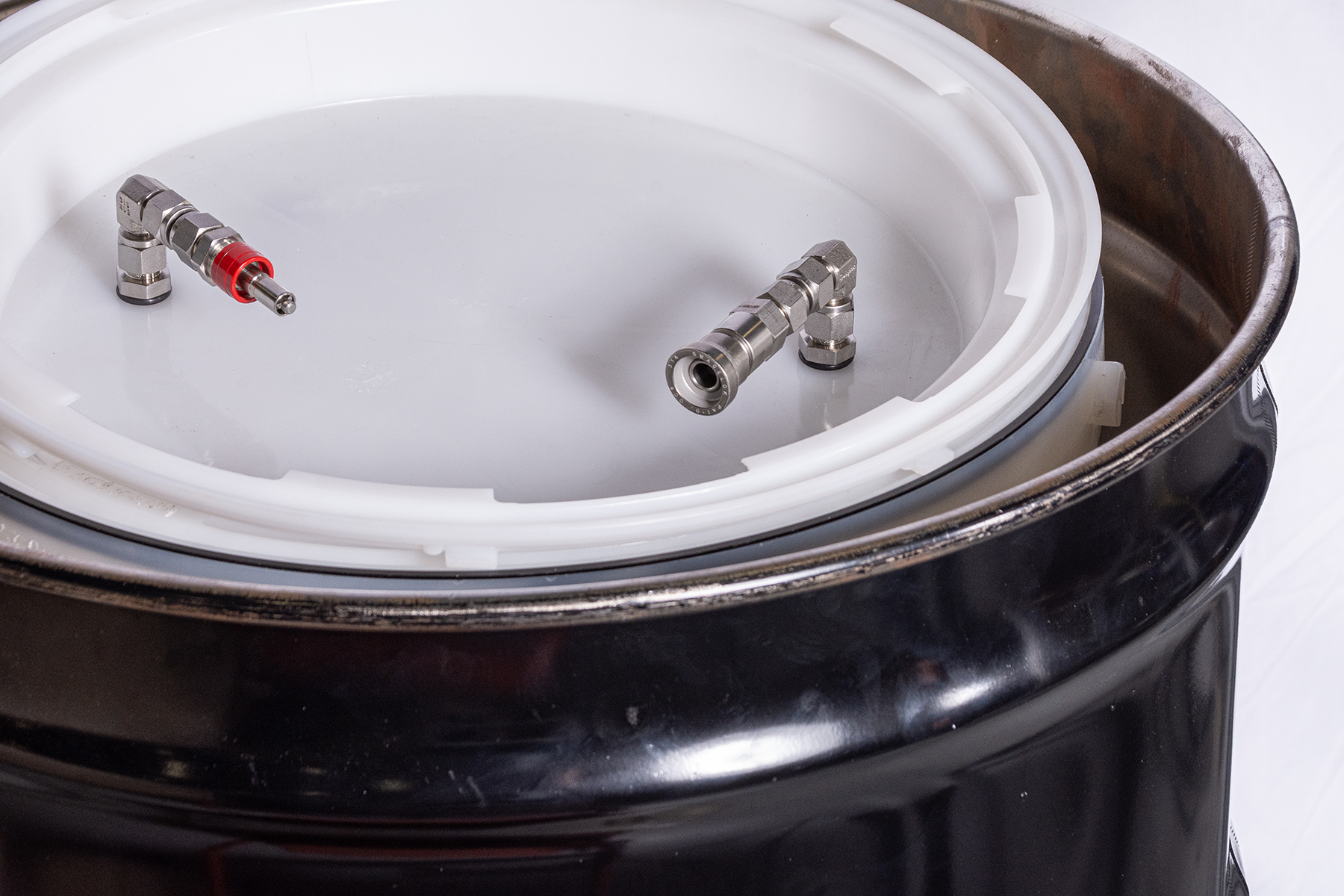
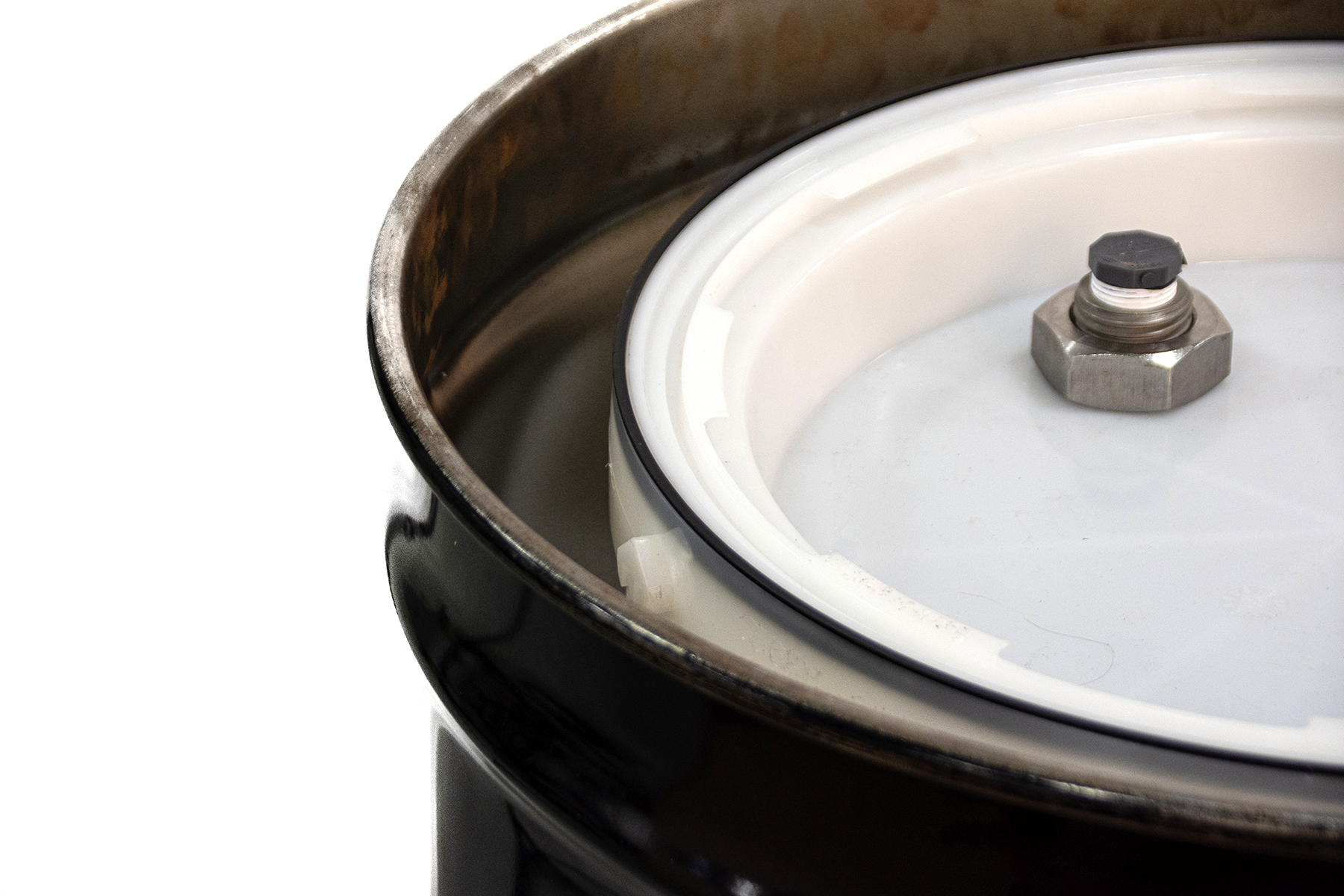