A view of the entrance to tower #22, showing the dismantled part of an inclined column.
While the construction of two additional reactors at Slovakia’s Mochovce nuclear plant (Units 3 and 4) may get most of the attention, it isn’t the only major project underway there. In October of last year, plant owner Slovenské Elektrárne commenced the first phase of an effort to revitalize two of the four 125-meter-tall, Iterson-type cooling towers that serve the facility’s two operating reactors—both of which began generating electricity in the late 1990s. Towers #11 and #21 had been refurbished in 2011 and 2012, respectively. The other two, however, towers #12 and #22, had never undergone refurbishment.
October 15, 2021, 3:26PMNuclear NewsMatt Palamara, Ali Fakhar, Stephen Smith, Patrick Fabian, Nathan Lang, and George Holoman Neutron noise monitoring allowed engineers to observe and interpret vibration characteristics captured by neutron flux detectors. (Photo: PSEG/Westinghouse)
The nuclear industry has historically relied on intermittent ultrasonic test and visual inspections of pressurized water reactor components to identify and manage degradation. While this reactive approach has proven to be effective, imagine a scenario in which the degradation could propagate throughout the reactor internals, making a more proactive measure necessary to avoid a major enterprise risk to the plant. Could a utility identify the onset of degradation within the reactor internals during plant operation? If so, could a repair be developed prior to the next refueling outage to prevent additional, cascading degradation? That is exactly the situation that Public Service Enterprise Group (PSEG) and Westinghouse engineers were able to navigate over the course of the 2019–2020 operating cycle at Salem Unit 1, resulting in a tremendous success for the plant and a historic landmark in the nuclear industry, while earning the team a 2021 Nuclear Energy Institute Top Innovative Practice (TIP) award.
The plant’s Program Engineering Department head has overseen significant new technology implementations for maintenance.
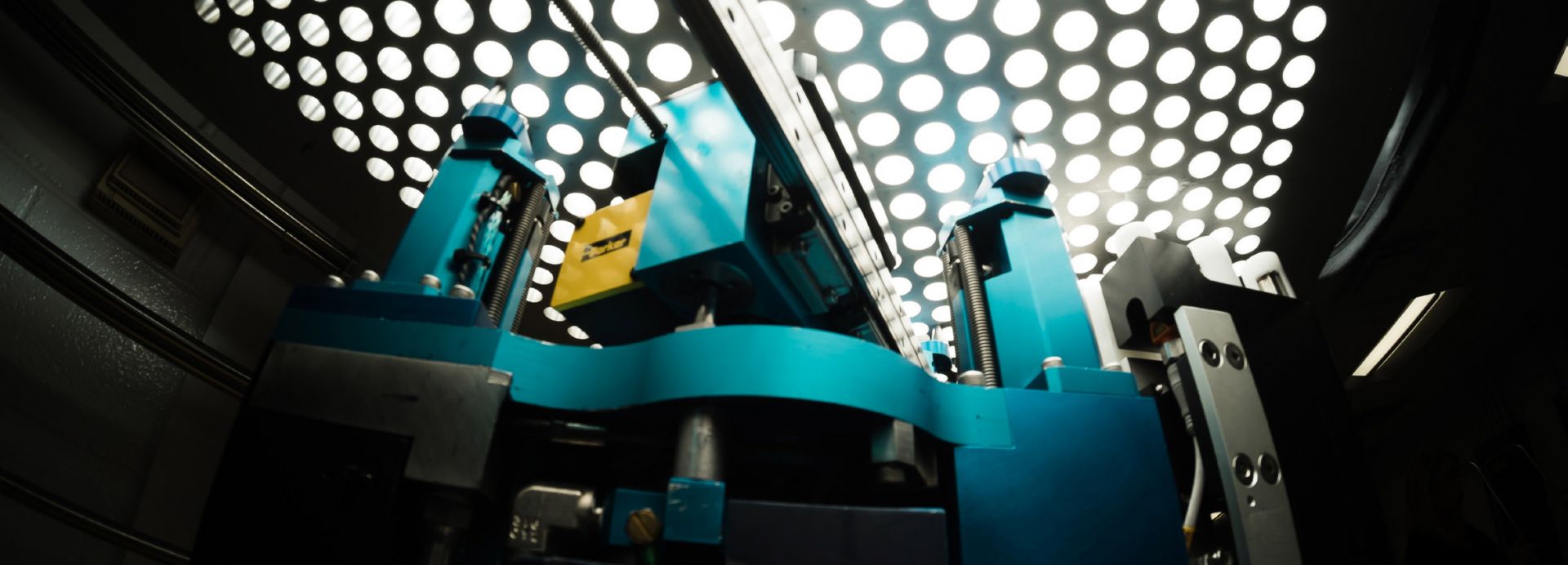
The Zephyr system uses probes for steam generator inspections. Photos: APS
The Palo Verde Nuclear Generating Station, a three-unit pressurized water reactor plant operated by Arizona Public Service Company, has started using an inspection technology relatively new to the nuclear industry. The technology, called smart pigs (an acronym for “piping inline gauges”), has previously been employed by oil and gas companies for inspecting and cleaning underground pipes. After testing and analyzing smart pig products from several companies, Palo Verde’s underground piping consultant, Dan Wittas, selected a smart pig suitable for navigating the tight-radius bends in the plant’s spray pond piping. The spray pond system consists of piping, a pump, and a reservoir where hot water (from the Palo Verde plant) is cooled before reuse by pumping it through spray nozzles into the cooler air. Smart pigs work by using the water’s flow through the piping to move an inspection tool within the pipe itself. The technology replaces the previous method of pipe inspection, in which various relatively small sections of piping were unearthed and directly inspected, and were considered to be representative examples of the overall piping condition. In contrast, the smart pigs obtain corrosion levels for the length of piping traveled through and allow a corrosion baseline to be established.